W miejscowości Hohenems w Austrii firma Kardex Mlog jako generalny wykonawca zbudowała dla specjalizującej się w systemach okuć i akcesoriów meblowych grupy GRASS magazyn wysokiego składowania o wysokim stopniu automatyzacji, który mieści około 38 800 miejsc paletowych. Do szczególnych cech należą w pełni automatyczny rozładunek pojazdów ciężarowych, wydajna kompletacja typu towar do człowieka z buforem dla osoby kompletującej zamówienia i dwa bufory dla towarów wychodzących. Punktem wyjścia dla tego ambitnego projektu budowlanego był konkurs pomysłów.
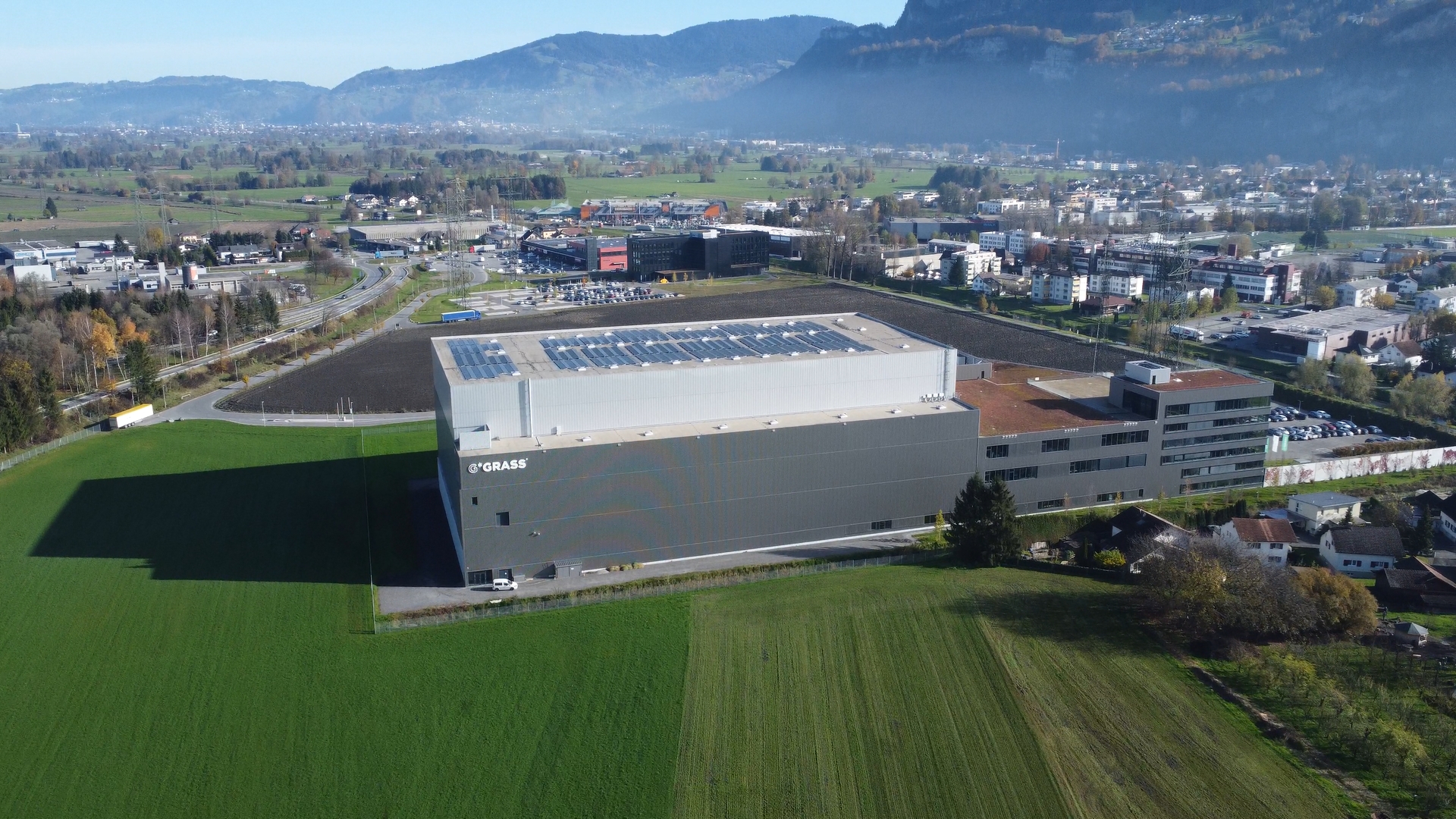
Delikatnie przesuwające się szuflady i elegancko zamykające się drzwi szafek: dzięki wyrafinowanym zawiasom, szufladom lub systemom podnośników do drzwiczek nowoczesne meble wnoszą swój wkład w wysoki komfort mieszkania. Na tym polu austriacka grupa GRASS oraz jej ponad 200 partnerów handlowych w 60 krajach należy do wyspecjalizowanych liderów. W celu uproszczenia procesów składania zamówienia i skrócenia czasów dostawy do klientów rozsianych na całym świecie, w 2020 roku dokonano centralizacji systemu logistycznego wyrobów gotowych dla wszystkich europejskich zakładów produkcyjnych w nowej lokalizacji w austriackim kraju związkowym Vorarlberg. Wcześniej zamówienia były wysyłane z czterech magazynów zewnętrznych, co prowadziło do wysokiej złożoności procesów.
Dobre doświadczenia wyniesione z innych projektów
Dlatego już w 2016 roku spółka GRASS GmbH należąca do grupy Würth zakupiła działkę o wielkości 52 000 metrów kwadratowych w okolicach Hohenems, aby zbudować na niej idealne centrum logistyczne. „Poszukując najlepszej koncepcji, rozpisaliśmy konkurs pomysłów, w którym wzięło udział osiem firm zajmujących się intralogistyką”, wspomina kierownik projektu Jürgen Moritsch. „Za Kardex Mlog przemówiły ostatecznie nie tylko dobre doświadczenia wyniesione z innych projektów w obrębie grupy Würth. Przekonali nas również bardzo zaangażowani pracownicy, a przede wszystkim spójne planowanie obejmujące liczne dobre pomysły na wysokowydajny przebieg procesów”, mówi Moritsch. Poza tym poszukiwano dostawcy, „z którym można by nawiązać długoterminową, partnerską współpracę, również w kontekście kolejnych projektów”.
Centrum dystrybucyjne na 38 800 miejsc paletowych zostało uruchomione 1 czerwca 2020 roku. Jest to do dziś największy budowlany projekt logistyczny, który został zrealizowany w austriackim kraju związkowym Vorarlberg. Firma GRASS zainwestowała w projekt 70 milionów euro.
Rozładunek zaledwie w 90 sekund
Już rozładunek pojazdów ciężarowych w obszarze przyjęcia towarów i następujący w dalszej kolejności załadunek do magazynu średnio 800 palet dziennie przebiegają tutaj w pełni automatycznie. Należy podkreślić, że system potrafi obsługiwać pięć różnych typów palet. Palety są dostarczane bezpośrednio z okolicznych zakładów produkcyjnych grupy GRASS jako część transportu zakładowego. Własne ciągniki siodłowe posiadają specjalne naczepy, których powierzchnie ładunkowe dysponują technologią przenośnikową ukrytą w podłodze pojazdu. Po zadokowaniu mobilny system przenośników zostaje połączony z systemem stacjonarnym i rozpoczyna się proces rozładunku – palety wyjeżdżają z pojazdów jakby poruszane niewidzialną siłą. „Po około trzech minutach naczepa jest pusta, a ciężarówka może ruszać w dalszą trasę”, podkreśla kierownik działu logistyki René Malojer. Kolejną zaletą szybkiego rozładunku jest fakt, że zgromadzone palety są znacznie szybciej dostępne dla klientów.
Każda paleta posiada kod QR, który jest automatycznie odczytywany w drodze do magazynu wysokiego składowania o jedenastu korytarzach i porównywany z danymi dostępnymi w systemie zarządzania towarami. „Wśród tych danych jest kod kreskowy informujący o typie palety. Zgodnie z tym oprogramowanie decyduje, w której części wysokiego regału należy szukać przestrzeni magazynowej”, wyjaśnia Manuel Bonner, który jako członek działu IT nadzoruje w firmie GRASS system zarządzania magazynem. W przypadku rozbieżności konkretne palety są automatycznie prowadzone na linię NOK (NOK = not ok) i tam automatycznie kontrolowane lub korygowane. Wszystkie pozostałe palety są bezpośrednio transportowane linią przenośnikową do punktu załadunkowego magazynu wysokiego składowania, gdzie są odbierane przez jedną z 11 układnic typu Kardex MSingle B 1000/34-ET i podnoszone na jeden z 22 poziomów regałowych. Zbudowane z jednej części układnice w lokalizacji Neuenstadt am Kocher przez Kardex Mlog mają 34 m wysokości i wykonują do 40 cykli kombinowanych na godzinę.
Zoptymalizowane pod kątem ergonomii stanowiska pobierania
75 procent ze wszystkich składowanych tutaj palet opuszcza magazyn ponownie jako palety pełne. Pozostałe 25 procent służy jako palety źródłowe do kompletacji typu towar do człowieka, która odbywa się w dwóch zoptymalizowanych pod kątem ergonomii stanowiskach pobierania. Te znajdują się na pomoście, który z poziomu parteru jest zaopatrywany w palety źródłowe przez osiem dźwigników nożycowych. Osoby kompletujące zamówienia mogą obsługiwać palety źródłowe warstwa po warstwie na optymalnej wysokości i układać pakunki na palecie docelowej za pomocą podnośników próżniowych. W celu zabezpieczenia operatorów podczas automatycznego procesu wymiany palet docelowych i źródłowych, każde stanowisko pracy jest wyposażone w kontaktowe maty bezpieczeństwa. Dopóki osoba zajmująca się pobieraniem produktów znajduje się w strefie zagrożenia, dźwigniki nożycowe są wyłączone. Puste palety są automatycznie dostarczane przez wózki do układania pustych palet i wózki do załadunku. Wbudowana waga rejestruje ciężar palet. Wszystkie puste palety są w jednoznaczny sposób oznakowane identyfikatorem palety.
Ponadto każde stanowisko kompletacji posiada ekran kontrolny i na stałe przyporządkowane mobilne terminale danych. Urządzenia są sparowane ze sobą na każdym stanowisku pracy, jak również w całym obszarze roboczym i komunikują się jako całość z technologią przenośnikową. Ekrany kierują czynnościami użytkownika w sposób wizualny, dostarczając mu jednocześnie przegląd multimedialny. W czasie rzeczywistym otrzymuje on szczegółowe informacje dotyczące aktualnego procesu pobierania i przydzielonych zadań. Ten łatwy w zrozumieniu system pozwala na zredukowanie o 80 procent czasu potrzebnego na szkolenie nowych pracowników zajmujących się pobieraniem. A to nie wszystko: „Dzięki temu już dotychczas niską liczbę błędów udało się zmniejszyć jeszcze o 70 procent i teraz oscyluje ona w obszarze promili”, podkreśla Jürgen Moritsch. Automatyczna kontrola ciężaru palety docelowej także przyczynia się do wyjątkowo wysokiej jakości procesu kompletacji.
Trzy magazyny buforowe na dopływ i wysyłkę towarów
Dostarczanie i odsyłanie palet źródłowych odbywa się za pomocą przenośników rolkowych, które stanowią element rozbudowanego systemu przenośnikowego. Palety docierają albo bezpośrednio z wysokiego regału albo z bufora dopływowego typu Kardex MSequence o wydajności 82 palety. Mierzący 12 metrów regał dopływowy znajduje się bezpośrednio za jednym z dwóch miejsc pobierania i jest w sposób w pełni automatyczny obsługiwany przez układnicę typu Kardex MSingle A. Przepustowość wynosi 43 cykle kombinowane na godzinę.
Dwa kolejne magazyny buforowe typu Kardex MSequence o łącznej pojemności 420 palet zostały zainstalowane w obszarze wysyłki towarów. Tutaj pracują dwie układnice typu Kardex MTwin S, które na podwójnej głębokości załadunku i wyładunku zapewniają przepustowość na poziomie około 54 cykli kombinowanych na godzinę, wstępnie sekwencjonując zaplanowane trasy. Wyładunek do 1500 palet dziennie następuje w ramach jednego zlecenia według zasady „najpierw lekkie, potem ciężkie”, aby zoptymalizować późniejszy załadunek. „Przy pomocy bufora towarów wychodzących możemy przeprowadzić pełny załadunek i odprawę każdej ciężarówki w czasie zaledwie 45 minut”, mówi René Malojer. Kierowcy przyjeżdżający do centrum logistycznego po wcześniejszej rejestracji otrzymują pager, na który przesyłane są informacje o rozpoczęciu załadunku i przyporządkowanej bramie załadunkowej. Zasadniczo wygląda to tak, że kompletny ładunek, składający się z maksymalnie 80 palet na jeden pojazd ciężarowy, jest przenoszony z wysokiego regału do bufora towarów wychodzących już dwie godziny wcześniej. „Dzięki temu możemy szybko zareagować także w sytuacji, gdy kierowca dotrze do nas wcześniej, niż było to planowane”, wyjaśnia Manuel Bonner.
Racjonalność, bezpieczeństwo i przejrzystość
Wnioski: wielość pomysłów i szczegółowe planowanie sprawiły, że firma Kardex Mlog wspólnie ze spółką GRASS GmbH zrealizowały wysokowydajne i przyjazne pracownikom centrum logistyczne. Zautomatyzowany w wysokim stopniu przepływ materiałów, ergonomiczna kompletacja oraz trzy zintegrowane magazyny buforowe sprawiły, że potrzebny personel udało się ograniczyć do 17 pracowników. Jednocześnie zwiększono jakość i szybkość dostaw, a przebieg całości procesów można śledzić w sposób całkowicie przejrzysty.
Tło: systemy okuć i akcesoriów firmy GRASS GmbH
Grupa GRASS to działająca na arenie globalnej grupa przedsiębiorstw, która jako partner rozwojowy i dostawca systemów dla przemysłu meblowego specjalizuje się w systemach okuć i akcesoriów meblowych. Portfolio obejmuje systemy prowadnic i szuflad oraz zawiasów i podnośników do drzwiczek. Założone w 1947 roku przedsiębiorstwo z siedzibą w Höchst (Vorarlberg, Austria) zatrudnia w swoich 19 lokalizacjach prawie 1800 pracowników i ma ponad 200 partnerów handlowych w 60 krajach. W 2021 roku firma GRASS wygenerowała obrót w wysokości 467 milionów euro. Od 2004 roku firma GRASS jest częścią grupy Würth.
O firmie Kardex Mlog
Kardex Mlog (www.kardex.com) z siedzibą w Neuenstadt am Kocher jest jednym z wiodących dostawców zintegrowanych systemów transportu wewnętrznego i magazynów wysokiego składowania. Firma posiada ponad 55-letnie doświadczenie w projektowaniu, wykonywaniu i serwisowaniu w pełni zautomatyzowanych rozwiązań logistycznych. Trzy oddziały zajmujące się nowymi obiektami, modernizacją oraz obsługą klienta korzystają z własnej produkcji mieszczącej się w Neuenstadt. Kardex Mlog należy do grupy Kardex i zatrudnia 305 pracowników. Obroty firmy wyniosły 89 mln euro w 2021 roku.
Więcej informacji:
MLOG Logistics GmbH
Wilhelm-Maybach-Straße 2
74196 Neuenstadt am Kocher
Osoba kontaktowa:
Bartosz Jankowski
Phone: +48 726 555 669