Kardex Mlog was commissioned as general contractor by the GRASS Group, a specialist systems supplier to the furniture industry. The task was to build a highly automated high-bay warehouse with approximately 38,800 pallet storage spaces in the Austrian town of Hohenems. The new plant was to feature fully automatic truck-unloading, efficient goods to-person picking with a picking buffer, and two goods issue buffers. The starting point for the ambitious construction project was an ideas competition.
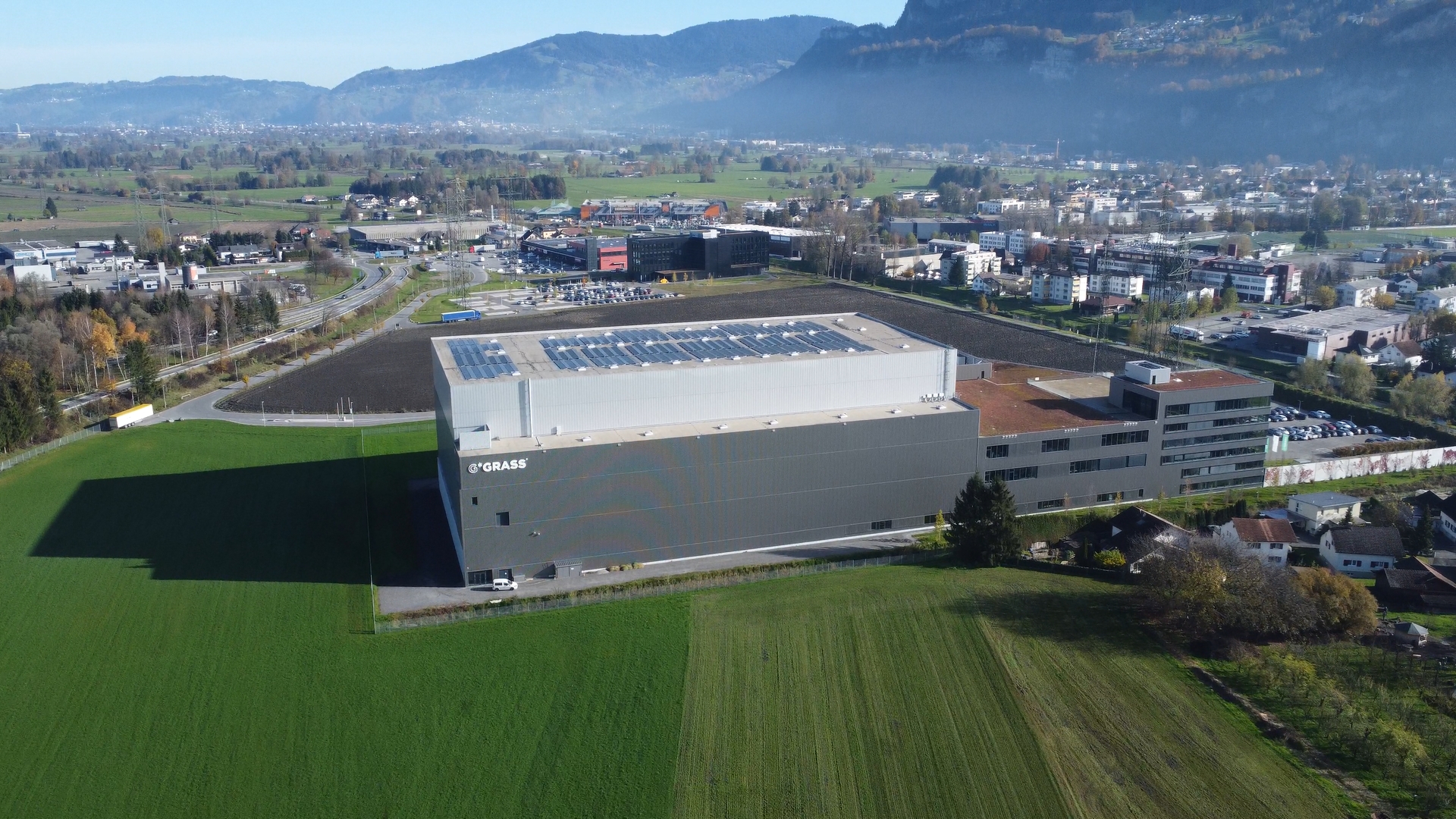
Smooth sliding drawers and elegantly closing cabinet doors: by utilizing clever hinges, pull-outs or flap systems, modern furniture significantly contributes to comfortable, high-end living. In this sector, the Austrian GRASS Group is a leading specialist with more than 200 sales partners in 60 countries. In 2020, to simplify order processing and reduce delivery times for customers worldwide, the GRASS Group centralized the logistics for finished goods at all of its European production plants to a new location in Vorarlberg, Austria. Previously, orders were handled at four external warehouses, adding complexity to already intricate processes.
Good experience with past projects
As early as 2016, GRASS GmbH, part of the Würth Group, purchased a 52,000-square-meter site in Hohenems to build an optimal logistics center. “In the search for the best concept, we launched an ideas competition in which eight intralogistics systems providers participated,” remembers Jürgen Moritsch, the project manager. “A major factor in Kardex Mlog’s favor was the good experience we had had already with other projects within the Würth Group. We were also very impressed by the commitment of the Kardex employees and, above all, by the thorough planning with numerous great ideas for highly-efficient processes,” says Moritsch. As well as that, the client was looking for a provider “with whom we could establish a long-term partnership of equals with a view to subsequent projects.”
The distribution center with its approximately 38,800 pallet storage spaces was commissioned on June 1, 2020. As of today, it is the largest logistics construction project to completed in the Austrian state of Vorarlberg. The investment by GRASS totaled 70 million euros.
Unloading in just 90 seconds
Unloading trucks at the goods receipt area and the subsequent storage of approximately 800 pallets per day runs 100 percent automatically. The system can handle five different pallet types. The pallets are delivered as part of an in-plant transport directly from GRASS Group’s surrounding production locations. The company’s own semi-trailer trucks have special trailers where the truck bed has a conveying system sunk into the floor. When a truck docks, the mobile conveying system connects to the stationary conveying system and unloading begins – the pallets roll off the truck as if by magic. “Within about three minutes the trailer is empty, and the truck can continue its journey,” explains logistics manager René Malojer. Another advantage of this rapid unloading is the pallets received are available faster for the customers.
Each pallet is allocated a QR code, which is read automatically on the way into the eleven-aisle high-bay warehouse and is compared with the data in the merchandise information system. “The information contained in the barcode includes the pallet type. Based on this, the software determines which section of the high-bay warehouse in which to seek a storage space,” says Manuel Bonner who, as a member of the IT department at GRASS, looks after the warehouse management system. If there are any discrepancies, the relevant pallets are automatically diverted to a “Not OK” (NOK) route where they are manually assessed and corrected. All other pallets are transported directly via a conveyor to the entry point to the high-bay warehouse, where they are received by one of the 11 stacker cranes of type Kardex MSingle B 1000/34-ET and are placed on one of the 22 racking levels. Kardex Mlog manufactures the one-piece stacker cranes at its company headquarters in Neuenstadt am Kocher, Germany. They are 34-meters high and have a capacity of 40 double cycles per hour.
Ergonomically optimized picking stations
75 percent of the pallets stored leave the warehouse subsequently as full pallets. The remaining 25 percent serve as source pallets for goods-to-person picking, which takes place at two ergonomically optimized picking stations. These stations are located on a platform supplied with the source pallets from the ground floor via eight scissor lift tables. The picking personnel can access the source pallets at an optimal height for each layer and use vacuum lifters to place the packages on the target pallets. Each workstation is equipped with touch-sensitive safety mats to safeguard the operators during automatic moving of the source and target pallets. Empty pallets are provided automatically via pallet trucks and shuttle carriages. An integrated scale records the weight of the pallets. Each empty pallet is assigned a unique pallet ID.
Also, each picking station has a control screen and permanently assigned, mobile data capturing devices. The devices are connected at each station and across the entire work area. They communicate as a unit with the conveying technology. The monitors provide visual guidance to the user and also offer a multi-media overview. In real time, the user receives detailed information on the current picking operation and on the user’s worklist. This user-friendly system makes it possible to reduce training time for new pickers by 80 percent. And that’s not all: “We have managed to reduce the already-low error rate by a further 70 percent and this is now in the per-thousand range,” says Jürgen Moritsch. Automatic weight control of the target pallets is another factor contributing to the excellent quality of the picking operation.
Three buffer storage areas for replenishment and goods issue
Transport of the source pallets to and from the picking stations takes place via roller conveyors, which are part of the comprehensive conveying technology. The pallets come either directly from the high-bay warehouse or from a replenishment buffer of type Kardex MSequence with a capacity of 82 pallets. The 12-meter high replenishment rack is located immediately behind one of the two picking stations and is served fully automatically by a stacker crane of type Kardex MSingle A. The throughput performance is 43 double cycles per hour.
Two additional buffer storage facilities of type Kardex MSequence, with a total capacity of 420 pallets, have been installed in the goods issue area. Two stacker cranes of type Kardex MTwin are deployed here. They deliver a throughput of approximately 54 double cycles per hour with double-deep storage and retrieval, and they pre-sequence the planned routes. Retrieval of the up to 1,500 pallets daily is carried out in accordance with the “heaviest items first” principle in order to optimize the subsequent loading process. “Thanks to the two goods issue buffers, we can now fully load and dispatch each truck in just 45 minutes,” claims René Malojer. When they arrive at the logistics center, the preregistered drivers are given a pager that informs them about the start of the loading process and the assigned loading bay. Typically, the entire load of up to 80 pallets per truck is moved from the high-bay warehouse to the goods issue buffer two hours in advance. “This gives us the flexibility to act quickly if the driver turns up earlier than scheduled,” explains Manuel Bonner.
Efficient, safe and transparent
Summary: With a range of good ideas and detailed planning, Kardex Mlog worked together with GRASS GmbH to construct a highly efficient and employee-friendly logistics center. With the largely automated material flow, the ergonomic picking process, and the three integrated buffer storage facilities, it was possible to reduce personnel requirements to 17 employees. At the same time, the quality and the speed of delivery were improved, and all workflows can now be tracked with full transparency.
Background: GRASS GmbH movement systems
The GRASS Group is a globally active group of companies, which serves the furniture industry as a development partner and system supplier and specializes in movement systems. The portfolio includes drawer and slide systems as well as hinge and flap systems. The company, which was founded in 1947 and is based in Höchst (Vorarlberg, Austria), employs some 1,800 people at 19 locations. It has more than 200 sales partners in 60 countries. In 2021 GRASS achieved revenues of 467 million euros. Since 2004, GRASS has been part of the Würth Group.
About Kardex Mlog
Kardex Mlog (www.kardex.com), with its head office in Neuenstadt am Kocher, Germany, is one of the leading suppliers of integrated material flow systems and high-bay warehouses. The company has more than 55 years of experience in the planning, implementation and maintenance of fully automated logistics solutions. The three business sectors - Greenfield installations, Refurbishment, and After-sales service – draw upon its in-house manufacturing facility in Neuenstadt. Kardex Mlog is part of the Kardex Group and employs 305 people. In 2021 the company achieved revenues of €89 million.
For more information:
MLOG Logistics GmbH
Wilhelm-Maybach-Straße 2
74196 Neuenstadt am Kocher
Press Officer:
Bettina Wittenberg
Tel.: +49 7139 / 4893-536