MAHLE Aftermarket automates DC in North America with AutoStore system from Kardex
20 January 2022, Company News
New construction / Automation
The AutoStore robotic storage solution will enable MAHLE Aftermarket to achieve outstanding customer service levels and quality goals on a global scale.
Montgomery, OH, January 20, 2022 – As a leading global parts and solutions provider to the Independent Aftermarket, MAHLE Aftermarket is seeing a shift in customer order profiles from larger pallet orders to smaller package orders in higher frequency. This results in an increasing number of shipping points per customer and shipping smaller quantities to more locations.
AutoStore is a fully automated and intelligent goods-to-person storage and retrieval system offering leading product storage density. Bins are stacked vertically in a grid and retrieved by intelligent, battery-powered robots that travel on top of the grid system, sorting, carrying and delivering bins to the respective workstations (ports), where a variety of warehouse operations can be performed (picking, replenishment, inventory control, etc.). The flexible, tailor-made system fits even the most unusually shaped facilities, allowing the grid to be placed around columns, on mezzanines and on multiple levels. The bins are stacked neatly on top of each other in a condensed grid-style system, increasing storage capacity up to four times and performance up to 10 times that of traditional storage methods, all without the need for additional workforce. AutoStore can easily adapt to changing order fulfillment requirements through a flexible configuration of the robots, ports and quantity of bin locations.
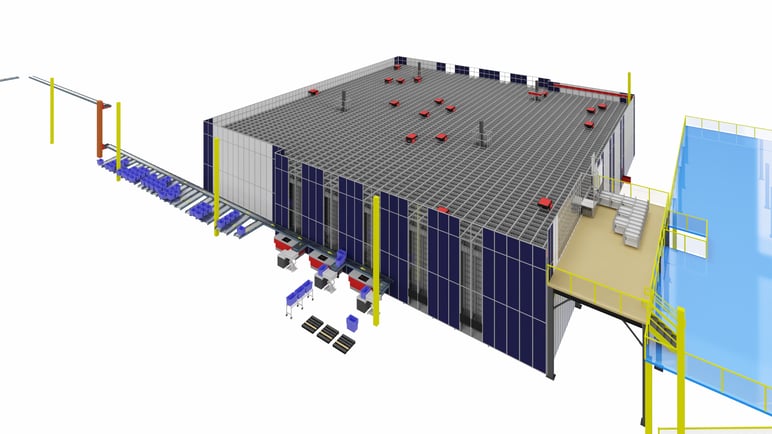
A global transformation
As a central core of MAHLE Aftermarket’s Digitalization and Automatization Strategy “Warehouse 4.0”, the Kardex AutoStore solution will enable the company to increase efficiencies and standardize operations on a global scale while achieving high customer service levels and quality goals.
![]()
|
“We chose Kardex for our AutoStore implementation because we were looking for an experienced partner with innovative strengths, intense customer focus, collaboration and a solid global presence with the ability to provide superior service coverage,” declared Georges Mourad, Director Global Operations and Business Excellence Aftermarket at MAHLE. “We are confident in facing the increasing challenges of the market with a flexible, sustainable and technologically advanced AutoStore solution that is capable of handling our growth for many years to come.” |
In the first stage, the AutoStore system in Olive Branch will contain 42,000 storage bins.
18 AutoStore R5 robots will sort, carry and deliver bins to 5 carousel ports and 2 conveyor ports serving as workstations for picking and replenishment. The ports will be linked directly to light goods conveyors for sortation to LTL and parcel outbound processing. The AutoStore solution will be integrated with the existing Warehouse Management System SAP EWM at MAHLE Aftermarket. Due to the modular design of AutoStore, performance and storage capacity can be expanded at any time, without impacting ongoing operations.
![]() |
“Our motivation to increase the level of automation in our warehouses came from a need to increase efficiency in order fulfillment, and a desire to provide our channel partners with the best service in the industry. The space-saving AutoStore solution from Kardex is able to provide the speed, precision, and reliability that our customers demand in today's fast-paced world”, concludes Jon Douglas, President Aftermarket North America at MAHLE. |
MAHLE Aftermarket, the business unit specializing in spare parts, uses the expertise from the series production of original equipment in its product range and supplies trade, workshop, and engine repair partners. The portfolio also includes products developed by MAHLE Service Solutions for workshop equipment as well as comprehensive services and customized training programs.
MAHLE Aftermarket is represented at 25 locations and other sales offices worldwide, with around 1,700 employees. In 2020, the business unit achieved a global sales volume of about EUR 898 million.
About Kardex
Contact
In case of any questions, please fill in our contact form.