Double-deep with no wasted space: Berner optimizes storage
15 December 2022, Company News
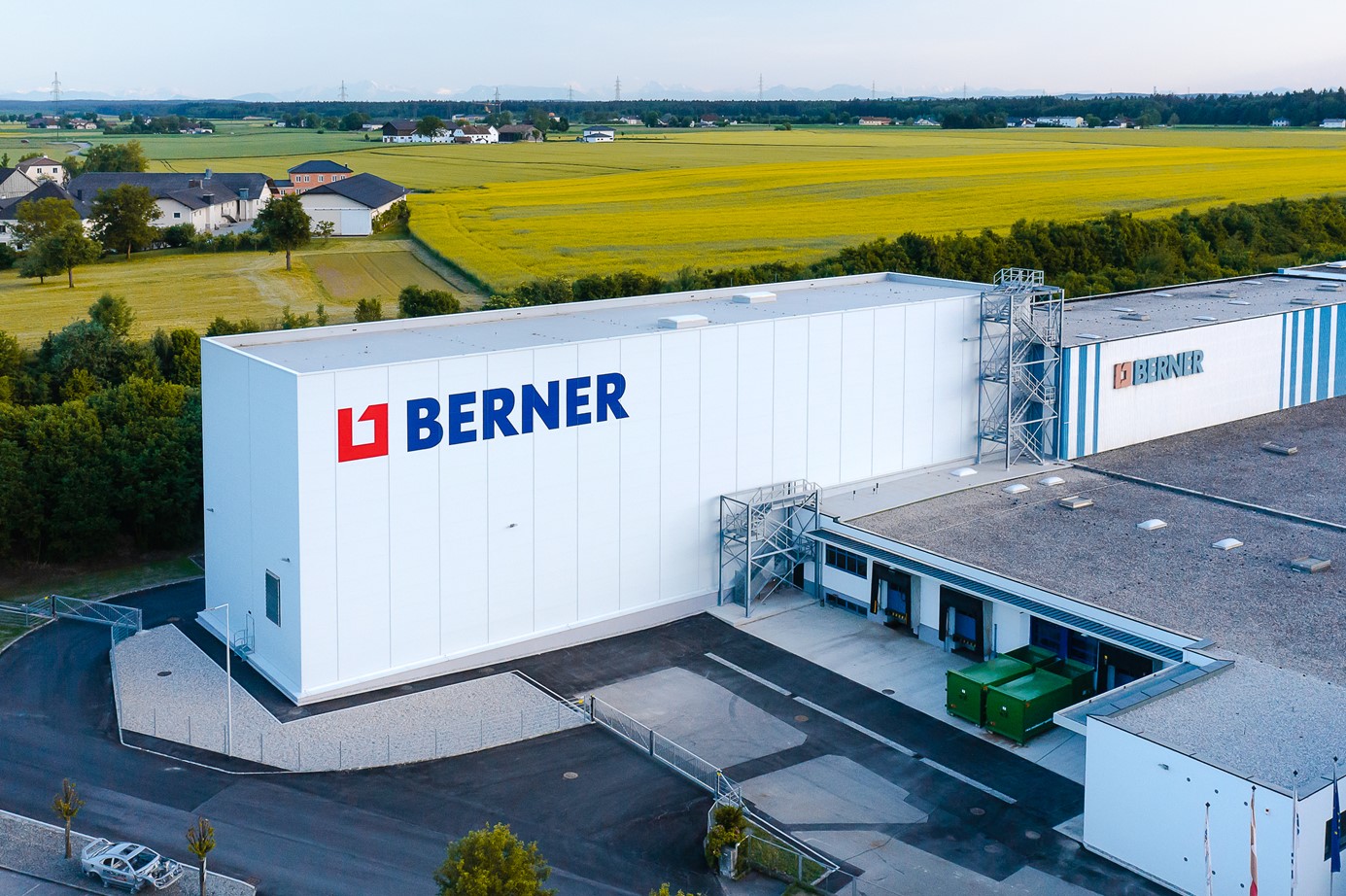
400 additional pallet storage spaces
“Over the entire height of the warehouse, there is a space gain of more than 1,800 mm per aisle,” states Kardex Mlog’s Andreas Koch, sales manager for Austria, who oversaw the overall project. “This allowed the creation of 400 additional pallet storage spaces, which would have been sacrificed in the second row if we didn't have Kardex MSpacer,” Koch calculates.
The Kardex MSpacer is equipped with extendable transverse sections that are otherwise only used in single deep storage. The height of the telescope that enters the pallet is dimensioned so that, in the rear row, the base clearance of the euro pallet is sufficient. This eliminates the requirement for costly depth supports, pads or vertically offset support beams in the racking, which incurs costs and reduces the usable storage space. The Kardex MSpacer therefore not only decreases operating costs but also production costs.
Kardex MSpacer
40 double cycles per hour
The forks of the Kardex MSpacer are designed for a payload of 1,000 kg in each case. Even in the second row, pallets of up to 800 kg can be stored. Acceleration and braking speed is 0.8 m/s². With single-deep storage and retrieval, the unloaded telescopes move at a speed of 80 m/min. Loaded, the speed is 50 m/min. In combination with the stacker cranes – with a travel speed of 180 m/min – this enables approximately 40 double cycles per hour or 66 single cycles.
Warehouse organization at Berner is carried out using a higher-level warehouse management system. For a picking operation, the relevant pallet is requested from the high-bay warehouse via the material flow computer and is assigned to the relevant picking station. The conveying technology controls ensure transport to the work station. After picking, the processed pallet undergoes a contour and load inspection. Using the weight determined in this inspection, the warehouse management computer carries out a plausibility check for the picking operation and triggers an optimized storage space search in the high-bay warehouse. Protruding boxes or other irregularities mean that the pallet is returned via the transverse shuttle. There, the pallet is checked and redirected.
Buffer line for 13 pallets
The pallets that are required at goods issue are requested by Berner’s higher-level warehouse management system. The host system sends the retrieval orders to the S7 controls of the stacker cranes. Conversely, every successful retrieval is reported to the host system so that, in the next step, the transport request can be passed on to the conveying technology control. Via the conveying system, the pallet to be retrieved is then transported to the goods issue buffer line, which can accommodate up to 13 pallets.
Using the Kardex MVisu plant visualization, the entire conveying technology and the stacker cranes and their operating status can be illustrated graphically. Visualization enables interactive contact with the material flow system - from context-related processing of location data to the information required in the event of a plant malfunction. A standardized interface connects the visualization system with the automation devices of the controls, which enables permanent data exchange between the systems.
Space for further growth
Kardex Mlog completed the entire project in just 12 months – project acceptance took place in December 2021. “The collaboration with Kardex Mlog was a partnership-based relationship, featuring high levels of competence and reliability,” says Hannes Huber, who is responsible for the supply chain and export areas at Berner in Austria. “With the innovative technology from Kardex Mlog, we now have a state-of-the-art high-bay warehouse, which provides approximately 5,600 pallet storage spaces with minimum footprint. This capacity means that we are well equipped for further growth,” adds Hannes Huber.
Background: Berner Ges.m.b.H
The Berner Ges.m.b.H. Company, based in Braunau am Inn, is the Austrian subsidiary of the internationally active Berner Group, one of Europe’s leading direct sellers of tools, equipment and materials for craftsmen and garages, and also for industry. About 500 employees, of which approximately 260 are sales agents, support customers throughout Austria. Also, the Braunau site supplies five Berner subsidiaries in Eastern Europe: Hungary, Czech Republic, Slovakia, Romania and Croatia. The Berner Group is a trading company with more than 8,000 employees at locations throughout Europe and its 23 European branches generate sales revenues of more than one billion euros annually. Berner Trading Holding GmbH has its headquarters in Künzelsau (Baden-Wuerttemberg, Germany) and in Cologne.
For more information, see www.berner.co.at.
About Kardex Mlog
Kardex Mlog (www.kardex.com), with head office in Neuenstadt am Kocher, is one of the leading suppliers of integrated material flow systems and high-bay warehouses. The company has more than 50 years of experience in the planning, implementation and maintenance of fully automated logistics solutions. The three business sectors - Greenfield installations, Refurbishment, and After-sales service – draw upon its in-house manufacturing facility in Neuenstadt. Kardex Mlog is part of the Kardex Group and employs 305 people. In 2021 the company achieved revenues of €89 million.
For more information:
MLOG Logistics GmbH
Wilhelm-Maybach-Straße 2
74196 Neuenstadt am Kocher
Website: www.kardex.com
Press Officer:
Tel.: +49 7139 / 4893-536