Kardex Mlog secures continuous replenishment in production
8 April 2024, Company News
Kardex Mlog has built two structurally identical, automated buffer storage plants for the BASF chemicals company. The new facility includes warehouse management and conveying technology to connect goods receipt and production. The two dynamic replenishment storage plants for raw materials each provide a capacity for 272 customized load carriers weighing up to 1,350 kilos and operate around the clock, seven days a week. The central component of the highly compact solution is the MTower-type lifting beam warehouse developed by Kardex Mlog, specifically designed for tall and narrow storage facilities. It operates via a shuttle car mounted on a vertically guided lifting beam. The automated pallet storage plant works faster and more efficiently than other storage concepts based on a stacker crane.
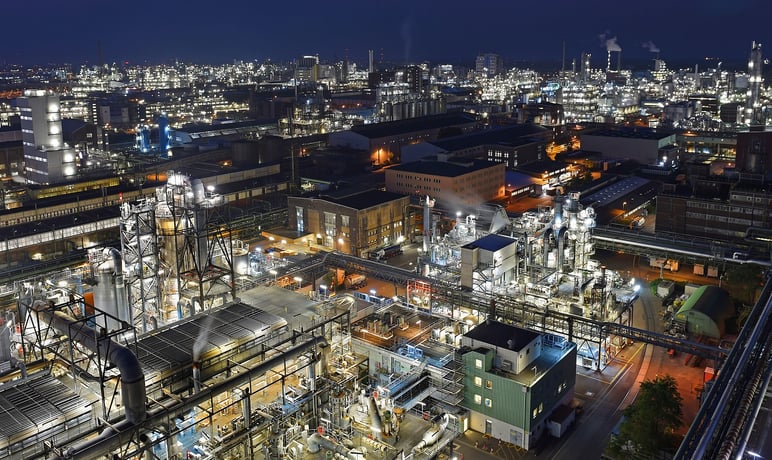
With the two new raw materials storage plants, BASF has decoupled its external inbound delivery from its production supply. The two identical Kardex MTower systems are in separate, adjacent buildings, and they enable automated raw materials supply to a production plant. “The main advantages of implementing the Kardex MTower solution were the extremely low floor space requirement and the variable construction height, which meant that we could make optimal use of the existing buildings,” explains Aaron Werner, an engineer at BASF SE. Both 24.7-meter-tall storage plants have a conveyor connection to two floors of the production facility, which means that no additional elevator is required.
The raw materials are delivered in big bags and, when placed into storage, these bags and the wooden pallets they are delivered on are placed onto plastic system pallets measuring 1,000 x 1,200 millimeters. Staging of the system pallets and their entire routing is handled fully automatically via the conveying system. The layout of these pallets was designed by Kardex Mlog in collaboration with BASF during the engineering phase, according to exact requirements. The result is that only clean and precision-fit system pallets are transported throughout the entire Kardex MTower facility and the conveying system. “This ensures a reliable operation and enables flexible use of the different load carriers, which sometimes differ significantly with regard to quality and norms,” according to Marco Burkhart, an engineer at BASF SE.
A forklift truck places the incoming raw materials on the waiting system pallets, which are then automatically transported away via the conveying technology. As they travel, the load units are subjected to a profile inspection and a weight check, and an automatic scanner collects the article data. The replenishment storage plants are operated by the Kardex Control Center, which includes Kardex WMS warehouse management, Kardex MVisu plant visualization, and Kardex MFlow material flow system – all solutions developed by Kardex Mlog. From the transfer point to Kardex MTower, the warehouse management system determines the appropriate storage space and creates the storage order. Up to 40 pallets can be stored per hour in this way.
At a height of approximately 19 meters, there is a work platform with two reception points and a collection point for packaging materials. The worker retrieves the big bags according to their requirements and unpacks and cleans them. They are then removed from the pallet by crane and passed on to production. Finally, the load carriers get transported to an empty pallet collector, where they are separated from the system pallet and collected. All pallets are stacked automatically and buffered in Kardex MTower until they are required in goods receipt or requested via the system.
The conveying technology, which Kardex Mlog also supplied, consists of 44 drive modules in each system. These include chain conveyors, roller conveyors, scissor lift tables, and corner transfers with lift tables. The scope of supply also included 300 system pallets, a semi-fixed rack sprinkler system, an aspirating smoke detector, four high-speed doors, four fire protection doors, and two manual racks on the ground floor with 32 pallet storage spaces.